Beijing DZEVERGREEN Jianshi Technology Co., Ltd. was established in 2021 and is a company focused on providing comprehensive supply services for the manufacturing industry. We are committed to efficient collaboration within the upstream and downstream supply chain, bringing tangible value-added benefits to our partners. Our services include:
- Supplier Screening and Integration: We help clients find the most suitable suppliers through strict evaluation standards to ensure product quality and delivery efficiency.
- Parts Supply and Assembly Services: We provide high-quality components along with professional assembly services to ensure the perfect delivery of the final product.
- Customized Parts Solutions: We offer tailored parts solutions based on specific client needs to meet various production requirements.
- Professional Support Services: Our team consists of experienced professionals who are always available to provide technical support and consulting services to clients.
- Quality Management Services: We are dedicated to ensuring that every link in the supply chain meets strict quality standards, helping clients enhance product quality and market competitiveness.
- Import and Export Agency Services: We provide comprehensive import and export agency services to help clients smoothly complete international trade and simplify complex processes.
We are constantly seeking collaboration with potential clients. Based on decades of supply chain work and management experience from our management team, we have established solid strategic partnerships with numerous manufacturing companies. Currently, we manage thousands of suppliers across various industries and supply thousands of components to our clients. You will gain a trustworthy partner, and together we will stride towards a successful future.
Services
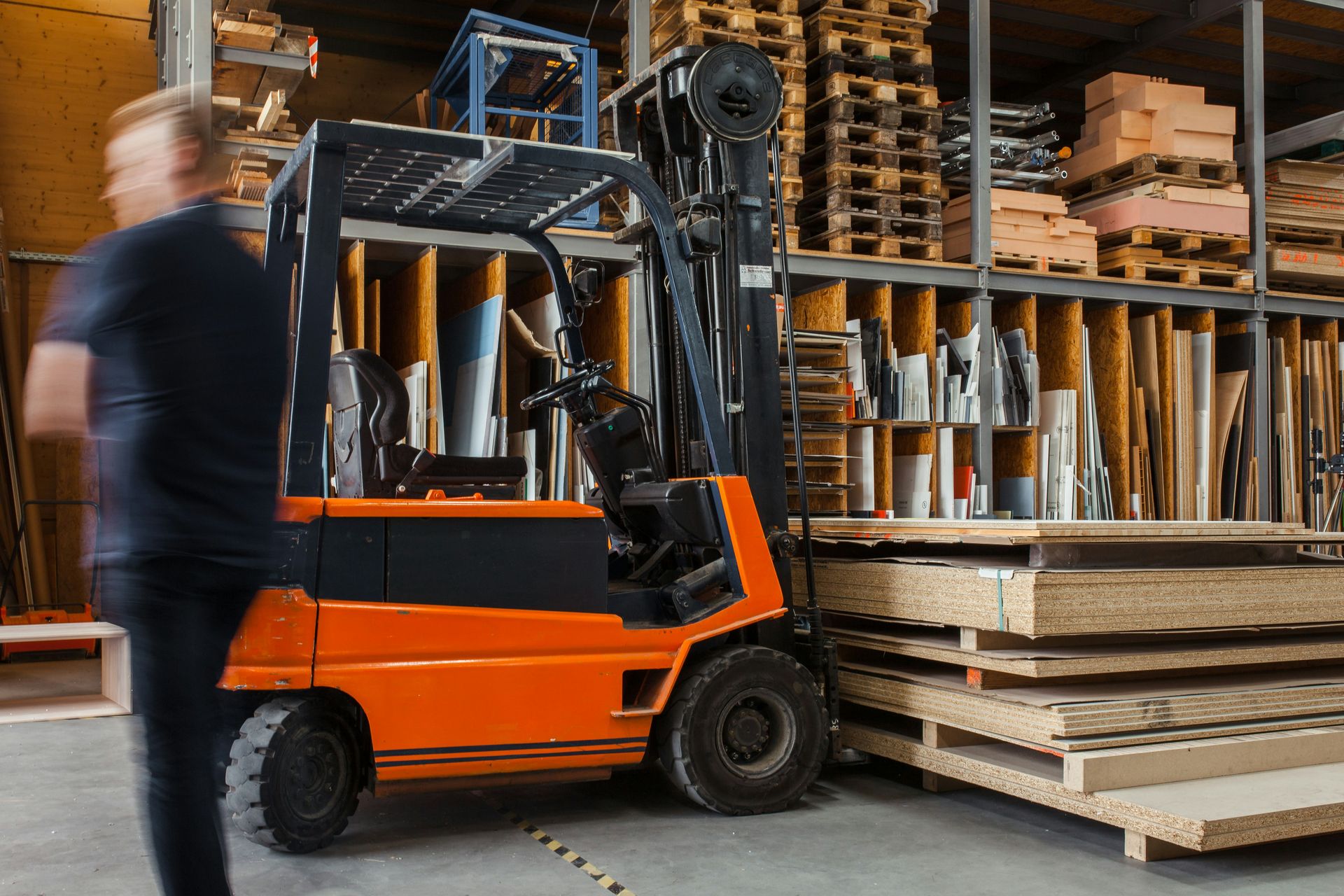
Supplier Screening and Integration
- Supplier evaluation and performance monitoring to identify and eliminate supplier supply risks.
- Strengthen supplier selection and collaboration to improve the stability and consistency of component supply.
- Integrate component types to enhance component standardization, reduce fragmented procurement, and lower overall supply chain costs, including management costs, production costs, and quality costs.
- By optimizing and integrating the supply chain and components, especially for edge procurement products, total supply chain costs can typically be reduced by 10-20% after simplifying supply chain operations and centralizing procurement to improve efficiency.
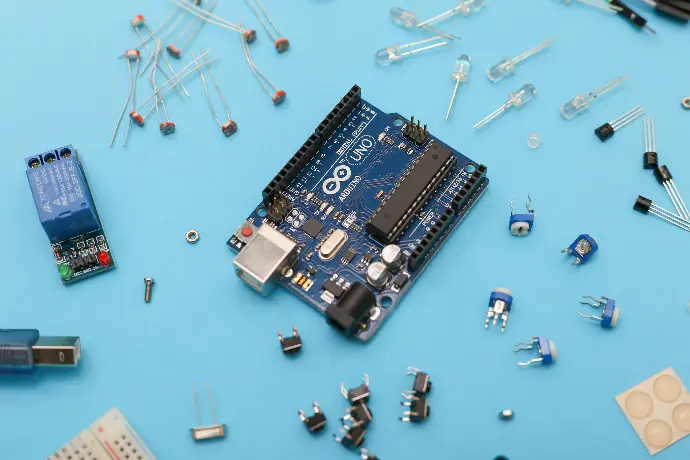
Product and Component Supply Services
- Rolling supply chain stocking planning and preparation based on customer demand planning.
- Ensure inventory availability, and we can provide inventory stocking support based on the customer's actual business situation.
- Optimize and integrate the supply chain to maintain efficiency and reliability for timely and accurate deliveries.
- Stable, safe, and timely logistics services are essential, and we always collaborate with the most reliable logistics providers in the industry.
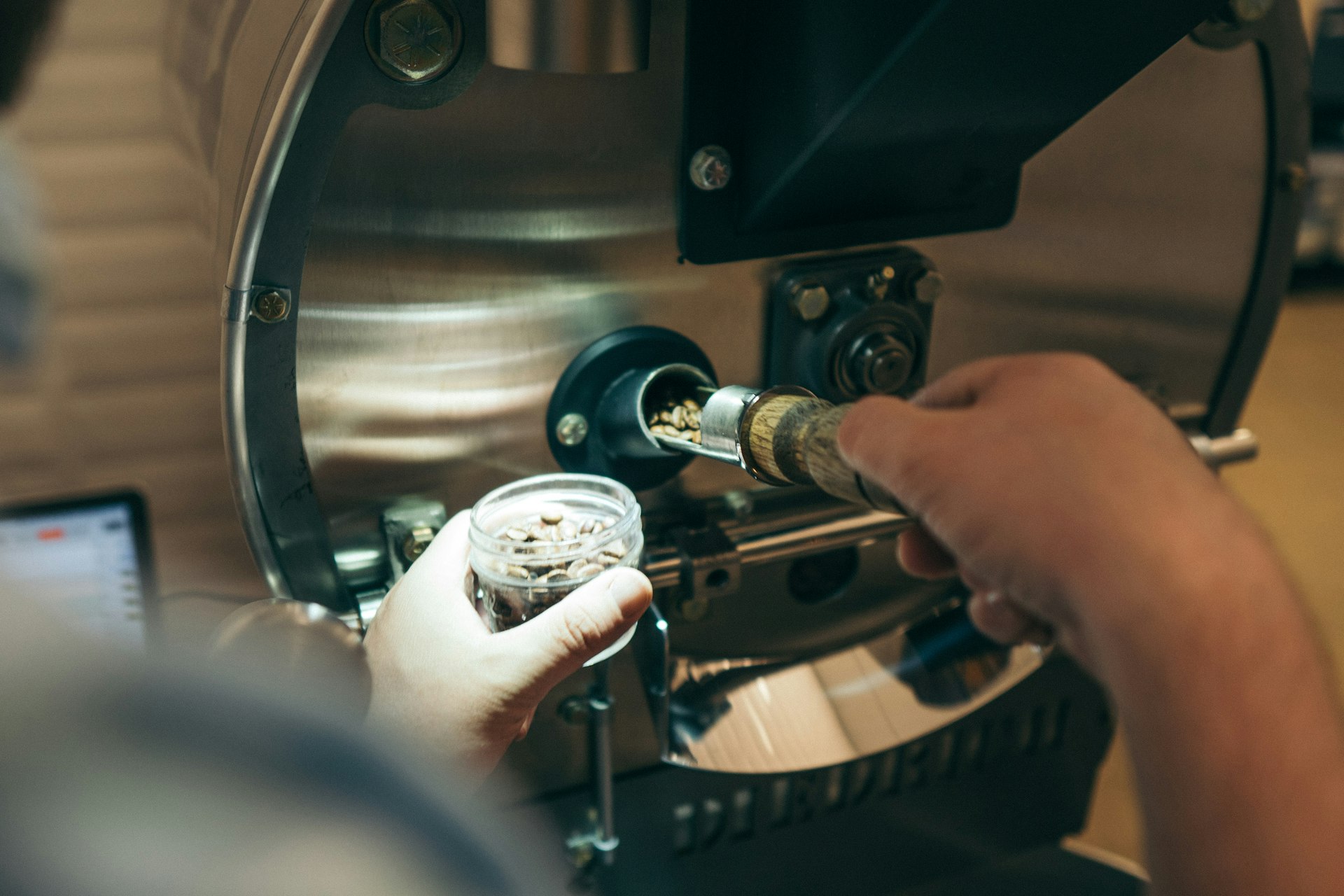
Quality Assurance
- We have a quality management system certified by ISO 9001:2015, conducting strict reviews of supply chain partners (such as IATF 16949, AS 9100, ISO 14001, and EMAS) to ensure that supplier qualifications and product quality meet design, production requirements, and environmental policies, thereby meeting customer expectations.
- Each batch of components undergoes batch quality inspections before delivery to ensure compliance with customer quality specifications and requirements.
- Imported products are rigorously reviewed for compliance with customer requirements, including PPAP, ROHS, REACH, and other projects, and relevant documentation such as product component guarantees is submitted.
- Internal and external audits, along with continuous improvement activities, are conducted to ensure the quality management system's effectiveness and compliance with customer quality requirements.
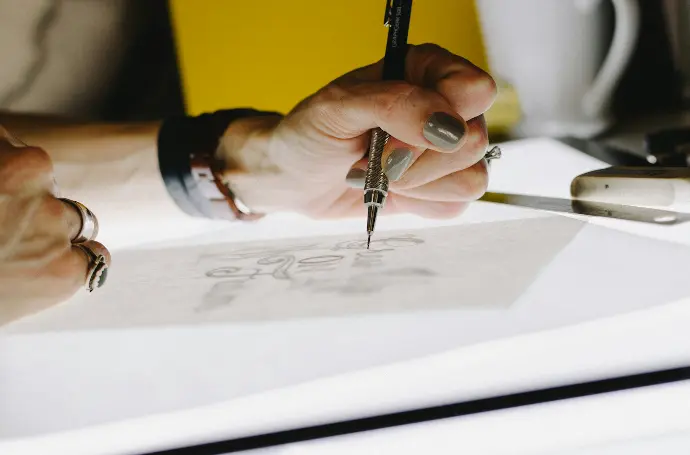
ESI Participation in New Product Component Design
- Provide technical support for Design for Manufacturing (DFM) of components, collaborating with customers in the early stages of product design to ensure optimization for efficient and cost-effective manufacturing processes. This includes considerations of material selection, manufacturing capabilities, assembly methods, and production feasibility and availability.
- Assess the lifecycle of market components and provide alternative suggestions for those nearing the end of their lifecycle.
- Assist customers in advancing the CE certification process for material substitutions.
International Business Agency
- Provide flexible international currency payment and collection services.
- Based on the customer's credit status, we offer payment credit support with terms of 2 to 6 months.
- Act on behalf of clients for the import and export transactions of products and components.
- We adhere to a good reputation and business practices, ensuring transaction security and convenience in managing payment processes.
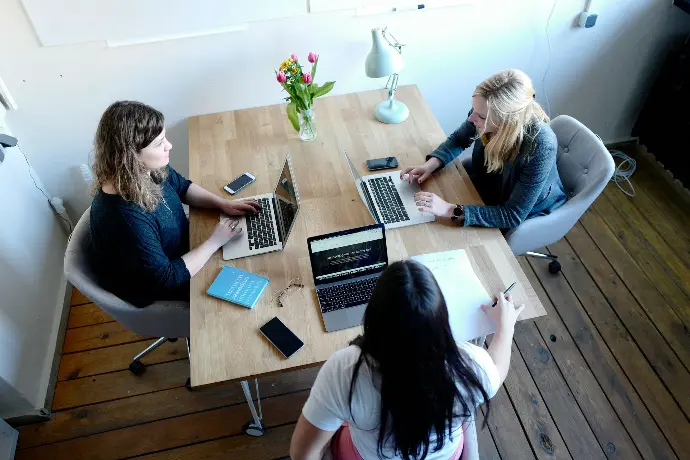
Professional Service Support
- Professional customer service personnel.
- Specialized technical coordination team.
- Always select top logistics service providers in the industry.
- Flexible service support.
- Professional enterprise resource management support system.